Maximizing Bottling Productivity with Smart Factory Solutions
Supply chain disruptions have increasingly challenged beverage manufacturers, undermining their operations and cutting into profits. According to the National Association of Manufacturers, nearly 80% of them have reported operational delays due to supply chain issues, with equipment inefficiencies cited as a major contributing factor.
Our client, a leading North American beverage manufacturer, experienced similar setbacks. Despite the strong market presence, their production was hindered by frequent equipment breakdowns and reactive maintenance practices.
Recognizing the need for a proactive approach, CES partnered with the client to implement an advanced machine monitoring solution. The alliance focused on turning operational challenges into opportunities, driving tangible improvements in efficiency and profitability through innovative, data-driven strategies.
Bottling Bottleneck: Addressing Machine Performance Inefficiencies
Before joining hands with CES, the manufacturer was wrestling with:
- Unplanned Downtime: Equipment breakdowns would halt production, often catching teams off guard and leading to missed targets.
- Costly Maintenance Cycles: Traditional diagnostic methods were reactive, involving manual checks that delayed responses, slowed production, and drove up operational costs.
CES worked closely with the client to address these challenges head-on, focusing on real-time data monitoring and predictive maintenance to turn insights into immediate actions.
The CES Solution: A Collaborative Approach to Machine Monitoring
CES deployed an integrated machine monitoring system that combined digital twins, AI-driven analytics, and real-time data dashboards. This setup allowed for a continuous pulse on machine health, turning raw data into actionable insights. The key components of the solution included:
- Process Twin Technology: Creating real-time digital replicas of each machine led to unprecedented visibility into equipment performance. Engineers could monitor every aspect of the machines, continuously updated with real-time data, quickly spotting any fluctuations or signs of wear that could lead to breakdowns.
These process twins provided a holistic view, combining data from multiple sensors to give a comprehensive picture of equipment health. This facilitated maintenance teams to shift from reactive to predictive maintenance, scheduling repairs and adjustments during planned downtime, which minimized disruptions. The result was a proactive approach that reduced unexpected breakdowns, streamlined resource allocation, and greatly improved overall operational efficiency.
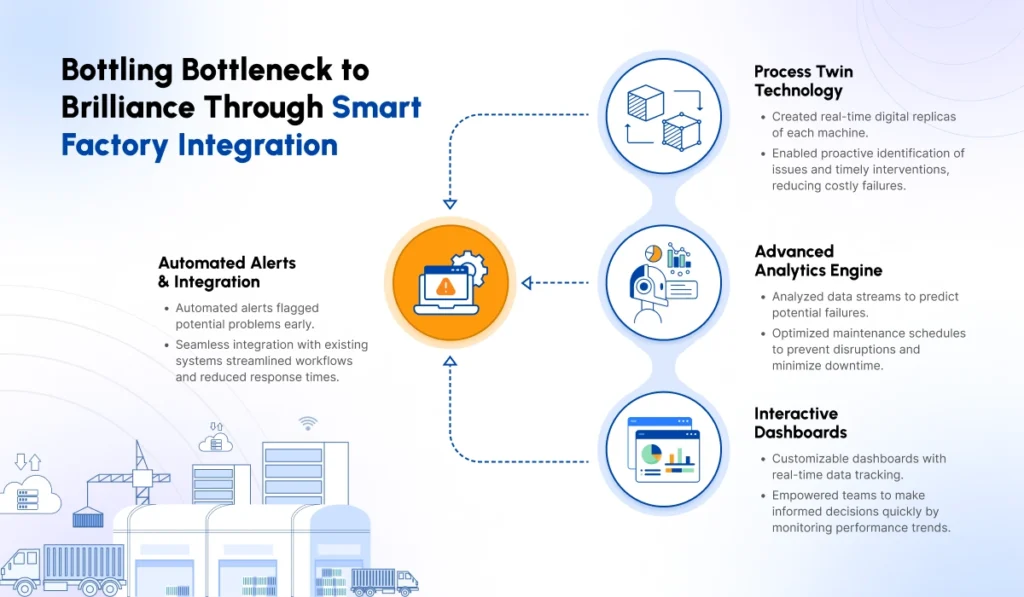
- Advanced Analytics Engine: Machine learning algorithms analyzed data streams to predict failures and optimize maintenance schedules. Instead of waiting for machines to break, teams could intervene early, preventing disruptions and slashing downtime.
- Interactive Dashboards: Introducing a headless BI framework with customizable dashboards, powered by streaming analytics, transformed data visibility. Engineers could zoom into metrics, track real-time performance trends, and make informed decisions on the fly. These visual tools kept information continuously updated, accessible, and actionable.
- Automated Alerts and Integration: The automated alerting and ticketing system provided timely notifications for maintenance needs, enabling teams to address issues before they became costly failures. Configured for conditional, predictive maintenance, the system tracked ‘Run Hours PM’ to generate alerts based on actual machine runtime rather than arbitrary intervals. This ensured preventive maintenance occurred precisely when needed, reducing unnecessary downtime.
Integration with existing maintenance software meant that alerts automatically generated service tickets, streamlining response times and aligning maintenance with production goals. By moving from calendar-based to condition-based alerts, the team could now target proactive interventions, cutting unplanned stoppages, optimizing resource use, and maintaining smooth operational flow across the plant.
Business Outcomes with CES: Bottling Success
The state-of-the-art machine monitoring strategy delivered impressive results, demonstrating the value of partnership and shared expertise:
- Improved Line Availability: The continuous monitoring system tracked over 5,000 data points per second, setting precise thresholds for conditional monitoring. This allowed targeted alerts for issues before they escalated, with predictive insights flagging abnormal trends like vibration and temperature shifts.
By transitioning to proactive maintenance, we increased uptime by 84%, reaching 98% within eight months. This high availability kept production lines running smoothly, meeting schedules, and keeping shelves stocked. - Boosted Productivity: Engineers spent less time on diagnostics, with a reduction of four minutes per machine health check. These minutes added up, translating to a 25% boost in overall productivity.
- Higher Quality Standards: Real-time monitoring helped identify and address quality issues before they escalated, reducing the scrap rate from 3.6% to 0.8%. This not only saved costs but also upheld the brand’s reputation for excellence.
- Faster Decision-Making: Engineers gained access to machine health data within 20 seconds, enabling quicker and more effective responses to potential problems. This prevented prolonged downtimes and ensured smooth operations.
- Significant Cost Savings: Through predictive maintenance and proactive problem-solving, the partnership generated sizeable savings, translating into a strong return on investment and reinforcing the client’s market position.
Final Thoughts
Our partnership with the beverage manufacturer went beyond resolving issues—it was about delivering long-term value. By cutting unplanned downtime by 84% and raising line availability to 98%, we didn’t just optimize operations; we transformed them. The results speak for themselves: a 25% boost in productivity and substantial savings. More than just fixes, they’re game-changing advancements that set new standards for bottling line performance.
Ready to turn bottling challenges into growth opportunities with cutting-edge machine monitoring? Let CES guide you to operational excellence. Contact our Strategic Client Partner at ankur.nair@cesltd.com to start the conversation.