Industry 5.0 Services for Smart, HumanCentric Manufacturing
Industry 5.0 merges human ingenuity with intelligent automation to deliver real-time responsiveness and sustainable innovation on the factory floor. Our comprehensive Industry 5.0 Services integrate collaborative robotics, IoT, digital twins, and AI to build agile, adaptive, and environmentally conscious production systems.
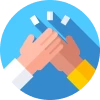
Trusted by 150+ tech first enterprises
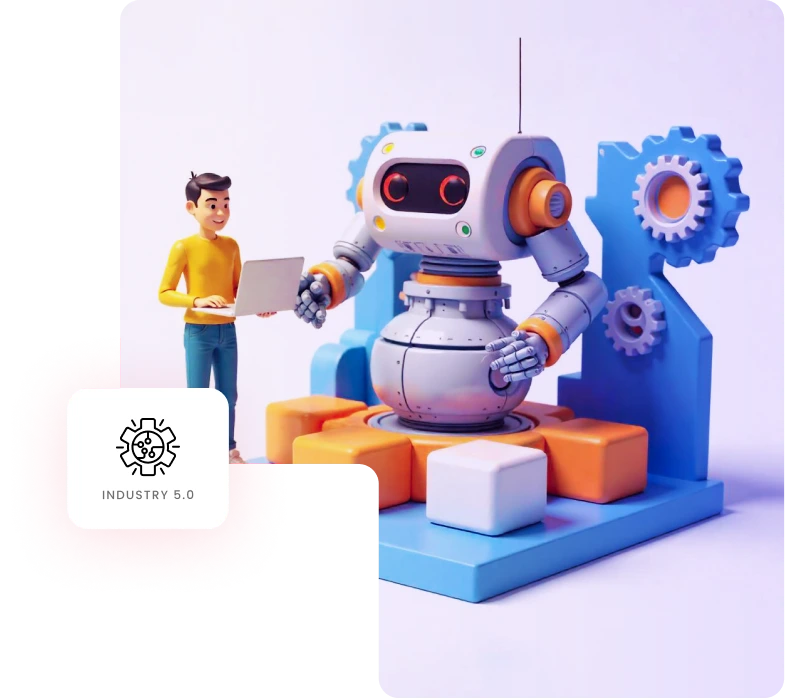
Empowered for the Smart Factory Shift
niche player in the 2024 Gartner® Magic Quadrant™ for f&a
Our Industry 5.0 Services are customized for the next-gen manufacturing landscape:
- Human + Machine Synergy: Cobotics and AI-powered workstations eliminate repetitive tasks while enhancing operator capabilities and precision.
- Connected Intelligence: IIoT, edge computing, and digital twins enable real-time visibility and responsiveness.
- Sustainably Smart: Smart energy systems, carbon tracking, and closed-loop waste processes deliver eco-efficiency.
Rooted in deep industry expertise, our strategies and solutions deliver measurable productivity, quality, safety gains, and ESG impact.
Our Industry 5.0 Service Offerings

Smart Factory Enablement
- IIoT & sensor integration across machines, lines, and utilities
- Edge computing nodes for low-latency, on-site decision making
- Automated quality inspection using computer vision algorithms
- Digital twin models for simulation, optimization, and control

Cobotics & Human–Machine Collaboration
- Collaborative robot (cobot) deployment on shop floors
- AI-powered task-assist systems for precision and support
- Ergonomics engineering for safer interactive workstations
- Digitization of operator workflows, KPIs, and feedback loops

AI, Machine Learning & Predictive Intelligence
- Predictive maintenance models to reduce unplanned downtime
- Adaptive supply chain and production optimization engines
- Real-time anomaly detection in process and quality variables
- AI-enabled process control systems (vision, sensor-driven, self-tuning)

Sustainable Manufacturing
- Smart energy monitoring and optimization
- ESG and carbon-footprint monitoring solutions
- Closed-loop waste systems for recycling and reuse
- Compliance dashboards, reporting, and analytics
Our End-to-End
Industry 5.0 Maturity Framework
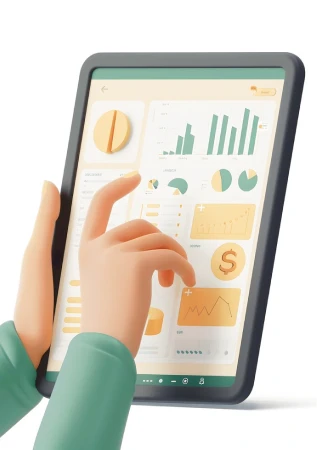
Connect
Deploy sensors, IIoT gateways, and edge compute
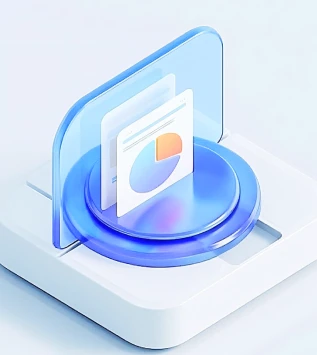
Model
Build digital twins and integrate cross-functional data
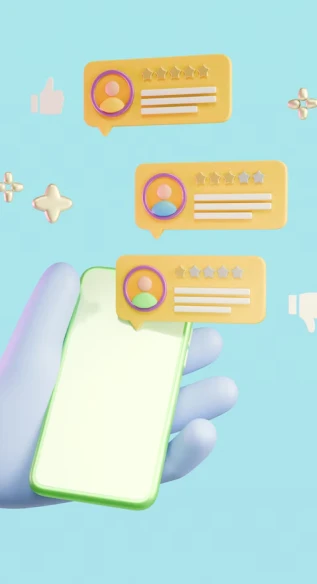
Collaborate
Implement cobots and AI-assisted workstations
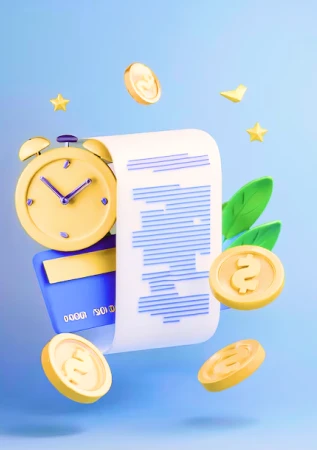
Predict
Enable real-time analytics, predictive maintenance
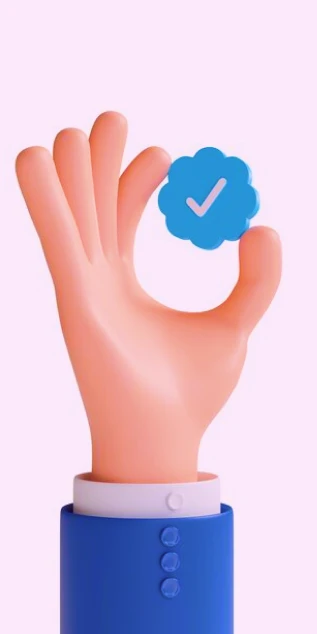
Sustain
Activate energy control, waste reduction, ESG reporting
Why CES for Industry 5.0?
Human-Centric Automation
Our focus is on empowering, not supplanting, human operators through collaborative robotics and AI.
Industry KnowHow
Proven deployments for Automotive, Pharma, FoodTech, Oil & Gas, and Industrial Equipment.
TechRich Ecosystem
Partners include ABB, KUKA, Siemens Edge, ThingWorx, Azure IoT, and Rockwell.
Measurable Gains
Efficiency, quality, safety, and ESG metrics embedded in strategy and delivery.
Sustainable Solutions
Smart manufacturing is aligned with circular economy and carbon accountability.
Why Invest in Industry 5.0?
- Improves human–machine synergy for safer, smarter production
- Optimizes factory operations with real-time data and automation
- Enables predictive maintenance and AI-powered decision-making
- Enhances product quality and process precision across lines
- Supports sustainable manufacturing and ESG compliance
- Drives innovation through IoT, cobotics, and digital twin integration
Case Studies
Rewriting Productivity on the Assembly Line
Explore manufacturing success stories where data, AI, and design thinking converge to elevate performance, precision, and sustainability.
View all Case StudiesFAQs
Industry 5.0 Services
Industry 5.0 blends human–machine collaboration, sustainability, and real-time adaptability with the automation and data integration of Industry 4.0 prioritizing people and eco-efficiency alongside performance.
Yes. We integrate IIoT sensors, cobots, and digital twins into brownfield environments using edge computing and non-intrusive automation, preserving uptime, and flexibility.
Typical results include a 20–40% reduction in defects, a 15–30% uplift in Overall Equipment Effectiveness (OEE), and meaningful reduction in energy per unit, with payback often seen within 12–18 months.
Our IIoT platform collects real-time telemetry from machines, feeding anomaly detection and predictive AI models to predict failures, flag maintenance needs, and reduce unplanned downtime by up to 50%.
Smart energy and waste monitoring often reduce carbon footprint and energy inefficiencies by >20% and closed-loop waste systems support recycling and ESG reporting.
Yes. Cobots are equipped with safety-rated features (such as ISO/TS 15066), and ergonomics and risk assessments are rigorously applied to protect operators in shared workspaces.
Industries with complex, diverse product lines such as Automotive, Pharma, Electronics, and Food experience the most rapid gains. Our expertise spans across all major manufacturing verticals.
Pilot deployments (e.g., sensor rollout + cobots) can run in 8–12 weeks. Full-cycle rollouts involving digital twins, analytics, and factory integration typically complete in 6–12 months.
Want to Deepen Your Understanding of Industry 5.0?
We’ve answered the most-asked questions on cobotics, IIoT integration, sustainability, and predictive manufacturing.
Industry 5.0 knowledge base